Is it Possible to Create a Factory with a Single Employee?
The Fourth Industrial Revolution is unlike the previous ones, as it won’t just reduce the number of jobs but it might actually do away with human labor altogether. The smart factories of the future could really have a single employee who’ll do more monitoring than actual work.
So, what really lies behind the concept of a smart factory? Find out in this article.
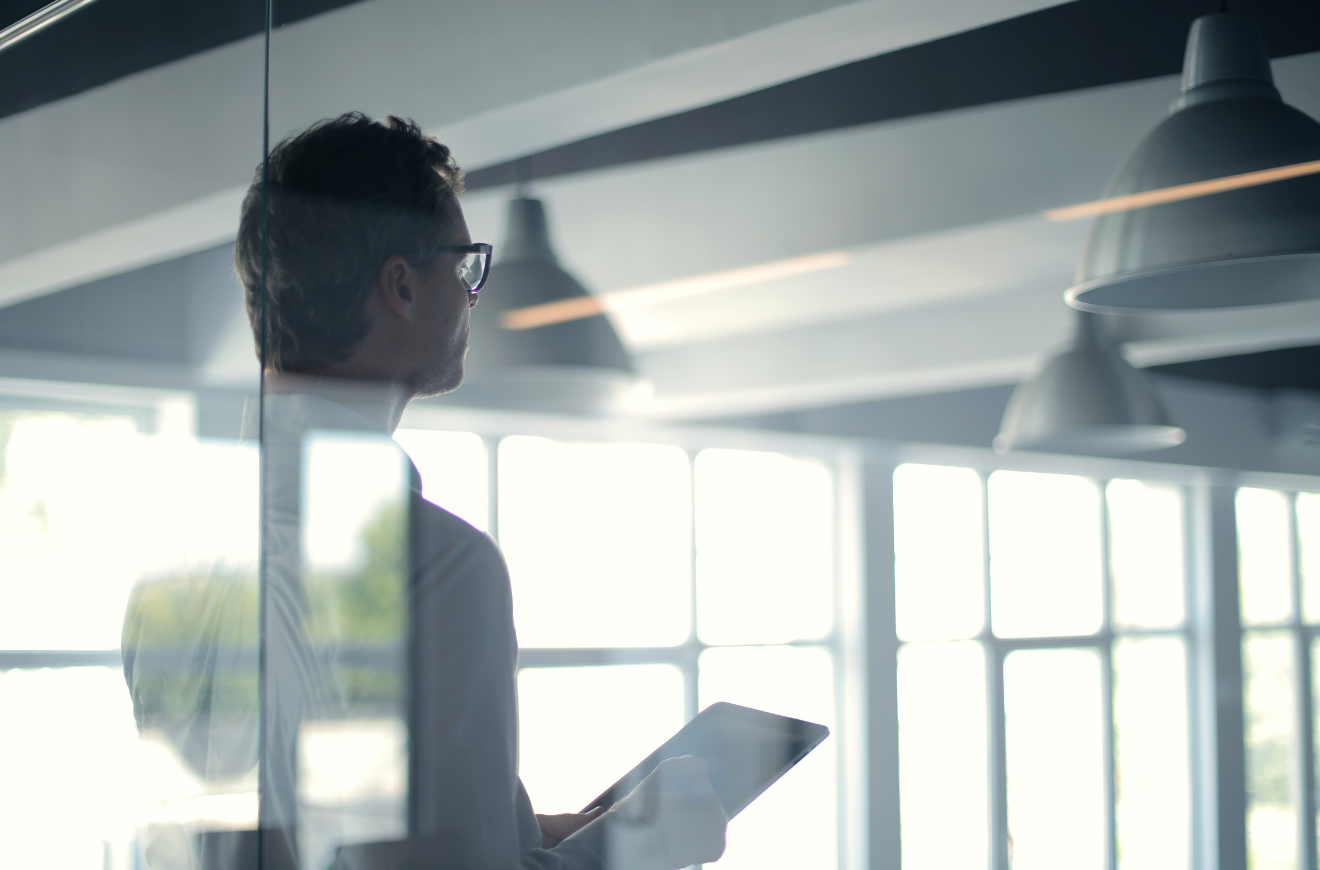
Is it Possible to Create a Factory with a Single Employee?
The Fourth Industrial Revolution is unlike the previous ones, as it won’t just reduce the number of jobs but it might actually do away with human labor altogether. The smart factories of the future could really have a single employee who’ll do more monitoring than actual work.
So, what really lies behind the concept of a smart factory?
Understanding the concept
Essentially, a “smart factory” presents a bridge between the digital and the physical world in order to optimize and more importantly, monitor the whole production process. The concept extends from supply chain management to manufacturing itself, including the operational staff.
Four main stages of handling data
A factory “learns” much in the way humans do: in stages. The first step a smart factory has to take is to analyze all the data available.
Then comes the proactive data analysis, which structures data to make it easily understandable. After the analysis is complete, the data becomes centralized, so it can be easily organized and visually presented when necessary.
Then AI and machine learning come into play to create better insights for human operators. We speak of “humans” but at this point, the whole process has become automated, so it can predict key issues and anomalies on its own.
Finally, a smart factory is ready to take action and solve problems without human intervention. As the human input decreases, a factory becomes “smart” in the true sense of the word.
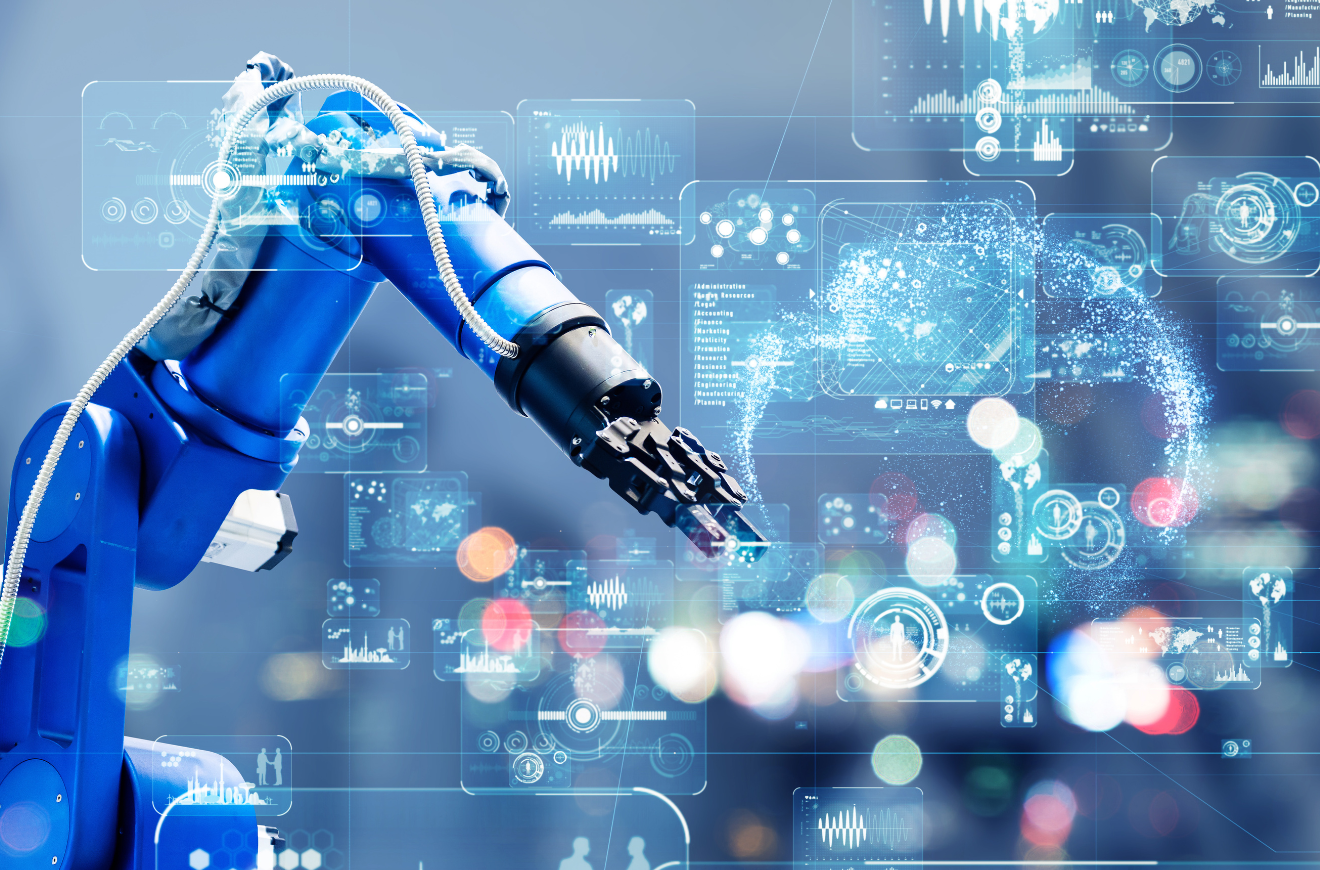
The technologies at play in smart factories
Industry 4.0, i.e. the aforementioned Fourth Industrial Revolution is comprised of several technologies that power the factories of the future.
Firstly, we have sensors on various machines and devices whose primary task is to collect the already-discussed data. Their secondary role is to monitor the production process, such as work temperature of individual machines.
Once the sensors detect that one or more variables are outside of the operating range, they alert the operator that action needs to be taken. Moreover, these sensors are part of a network that monitors several devices simultaneously.
Speaking of networking, cloud computing lies at the core of smart factories. Not only is such storing and processing of data cheaper but it is flexible as well. Large amounts of data can be stored in clouds for easier access in real-time.
Furthermore, virtual and augmented realities are used to organize products and maintain and repair equipment. AR can be used to overlay data across reality on a smartphone, while VR best functions using special glasses. Both methods give decision-makers insights that are far superior to hard-copy stats and figures of the past.
Finally, a smart factory is able to simulate performance using digital twins. By mimicking a process in the digital world, operators can cost-effectively implement improvements and enhance planning.
IoT as a crucial component of smart factories
Connecting devices through Internet data communications is nothing new but the Internet of Things is a lifeline for smart factories. Tracking and identifying improvements in the manufacturing process is executed using sensors, wireless connections, and programs for collecting data.
IoT reduces the physical demands on workers, making the production environment safer in the process. In addition, machine learning helps reduce energy consumption, protecting the environment without harming productivity.
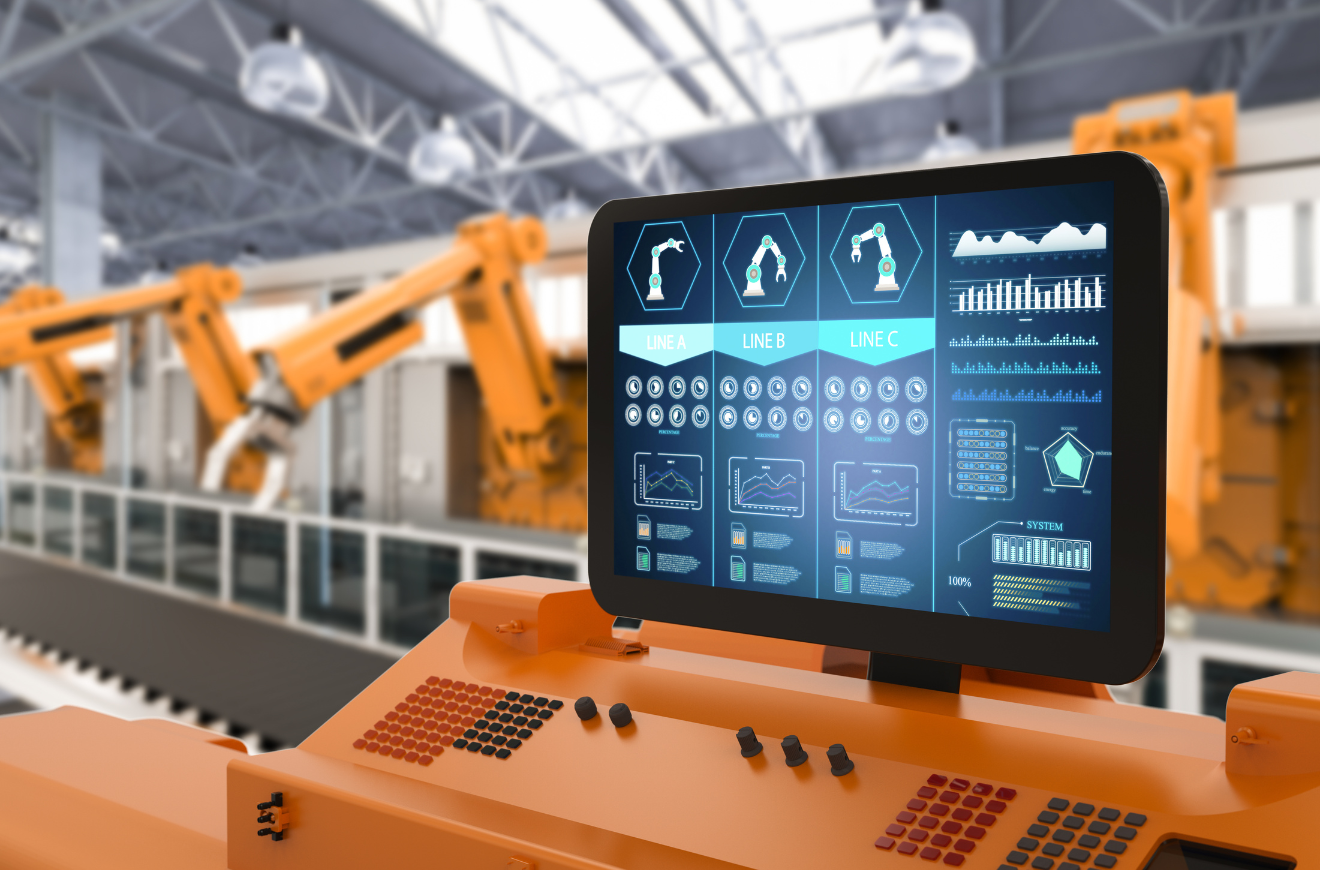
Is smart manufacturing sustainable?
Speaking of environmental protection, smart factories contribute to our planet’s “health” in several ways. For example, simulation software we’ve discussed earlier significantly reduces the amount of physical waste.
Moreover, computer simulations help find the most suitable materials that have a low carbon print. Finally, the buildings in which these factories are housed are designed and built as zero-waste structures that are connected to a smart grid.
For instance, a warehouse or a manufacturing plant with solar panels adorning its roof can generate power instead of consuming it. In this aspect, Industry 4.0 is not only cleaner that the previous industrial revolutions but it will actually clear up the fallout of the previous ones.
Will smart factories be profitable?
Protecting the environment is definitely something to strive for but a smart factory should be profitable before all. From improved product quality to enhanced worker safety, factories of the future are highly unlikely to end up in the red.
Governments in many countries have recognized smart factories as driving engines for national economies, so investors can count on grants and subsidies. Even without them, simple infrastructural aid, such as building an access road, is enough to make a smart factory profitable in the long run.
The issue of cybersecurity
Having listed all the benefits of smart factories, we must mention one possible downside to the process: cybersecurity. Since smart factories heavily rely on computing and digital systems, cybersecurity takes precedence, as privacy and the protection of data are vital for every business.
Data sharing lies at the heart of digitization but only when it’s intentional. Errors and hacker attacks loom over every smart factory, so investing in cybersecurity goes hand in hand with setting up a smart factory.
Investors who are looking to cut cost in this segment should give smart factories a wide berth, as they have failed to understand the concept fully.
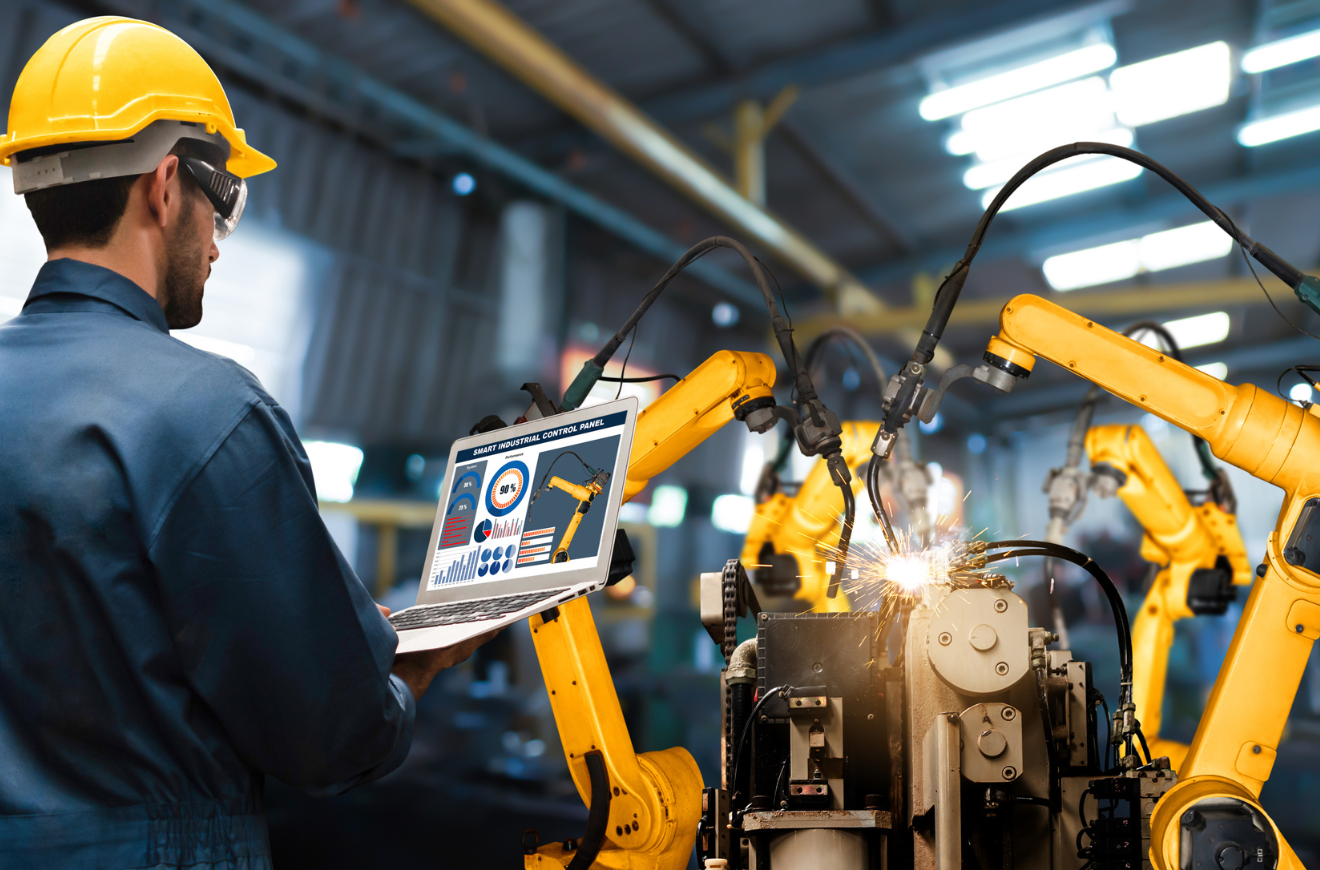
The bottom line: Will humans be needed anymore?
In industrialized nations, such as South Korea and Japan, it is already more profitable to have a robot perform a task instead of a human. However, most of these jobs aren’t the ones humans are fighting over.
Dangerous and mundane jobs in manufacturing will disappear due to automation, which is good news for human labor. Namely, constantly improving the manufacturing process requires hiring more high-skilled workers.
To summarize, menial jobs will disappear from smart factories but human experts will very much be needed for two reasons. Firstly, to continually upgrade the system and keep it safe from cyberthreats, and secondly, to monitor the production process.
And yes, for some industries, this means that at times, a single worker will oversee an entire factory, while artificial intelligence and robots will be doing most of the actual work.